Sustainable Corrugated Packaging & Displays
For Consumer Goods, E-Commerce & Food Products
Packaging solutions for your products and sector
Why you should buy packaging and displays from THIMM:
-
To make your products successful
At THIMM you will find the simplest and best solution for your products and your brand.
-
To be sustainable
THIMM produces packaging made from sustainable corrugated cardboard – an ideal circular product.
-
To ensure quality
With a minimum of input factors we achieve maximum quality and sustainability.
-
To take advantage of digitalisation
THIMM turns your packaging and displays into digital multi-talents.
-
To save time
Short delivery times for packaging and displays thanks to the digital value chain.
-
To get the best price
Buy directly from the packaging manufacturer THIMM and secure the best price.
Perfect packaging solutions for all industries and products
Our truly satisfied customers
Do you have any questions about packaging or displays?
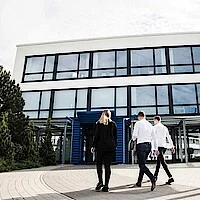
THIMM Verpackung GmbH + Co. KG
+49 5551 703 0
hallo@thimm.de
- Find out about THIMM!
- Get the simplest packaging solution for your products!
- We look forward to your enquiry!
Then call us directly on +49 5551 703 0, send us an email at hallo(at)thimm(dot)de or fill out the contact form.
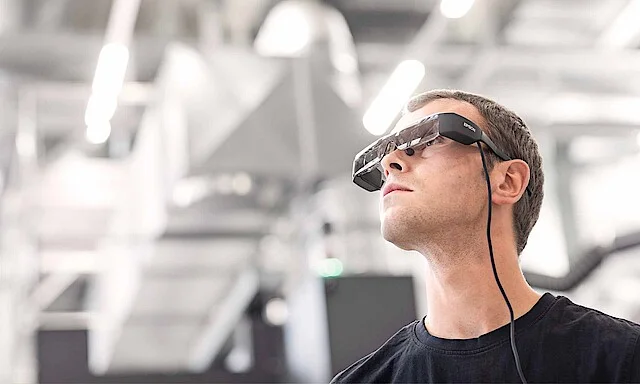
Digitalisation in the packaging sector
Internet of Packs
The Internet of Packs (IoP) combines real packaging with the virtual world by creating a completely networked and transparent supply chain. Digitally-printed packaging plays a particularly important role in this, as it enables seamless networking between the physical product and the digital world. Find out here about THIMM’s digitalisation vision.
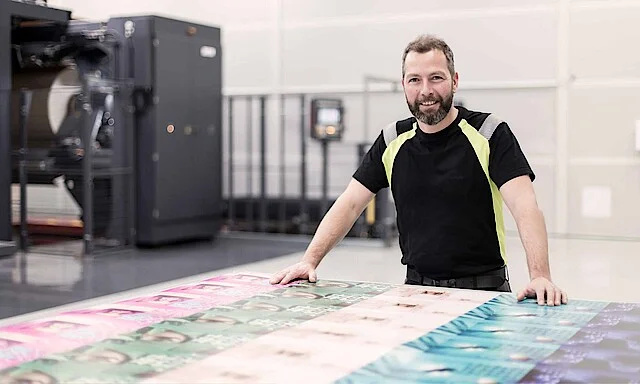
It’s impressive what printing can achieve
THIMM produces an impressively wide range of packaging printing. We have a state-of-the-art technology portfolio to cover all common printing processes. Find out about digital printing, flexo preprint/postprint and offset printing here. Learn everything about the advantages and uses of the different processes. THIMM turns your packaging into a digital multi-talent!
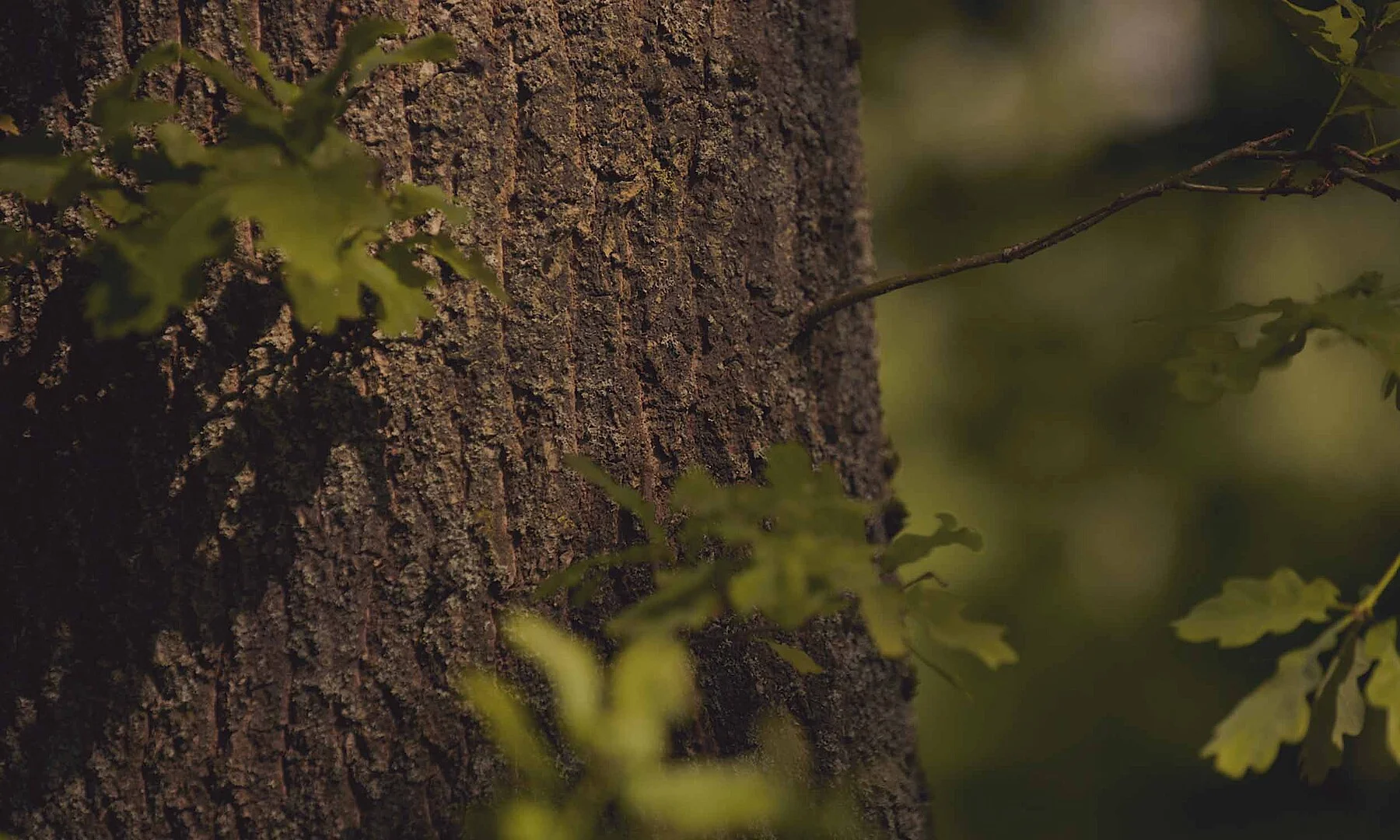
Sustainable packaging solutions from THIMM
With a minimum of input factors we achieve maximum quality and sustainability.
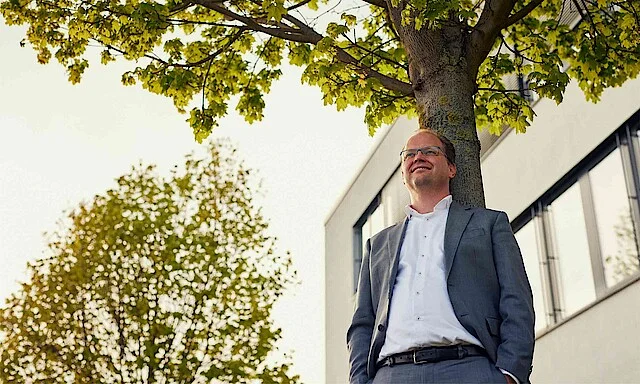
THIMM – Your sustainable packaging solutions provider
Packaging manufacturer for the consumer goods sector
Who is THIMM? We, the THIMM family business, have been the sustainable solutions provider for the packaging and distribution of consumer goods since 1949. Content is important to us. That’s why we want to constantly improve the packaging of our customers’ goods.
THIMM is an award-winner in the packaging sector
Quality and sustainability are important to us
Leading from the front with pioneering spirit and passion
How can we help you?
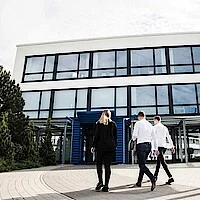
THIMM Group
+49 5551 703 0
info@thimm.de
You can reach us via the contact form, by e-mail to info@thimm.de or by telephone on +49 5551 703 0. We look forward to hearing from you!
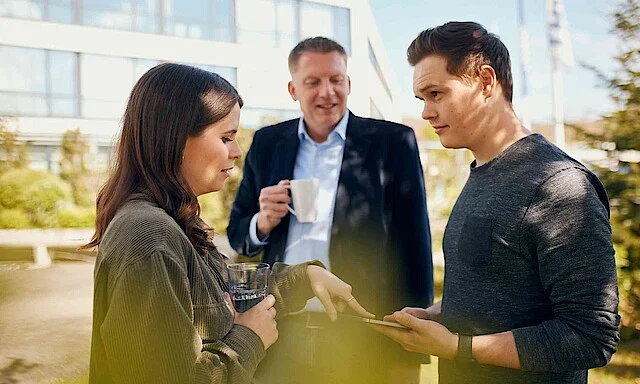
People at THIMM
Get to know our employees and their daily work at THIMM. At THIMM everyone can sense the spirit of a modern family business with its informal culture, mutual appreciation and pioneering attitude. The diversity of individual personalities, passions and experiences make working together at THIMM unique.
Career at THIMM
THIMM on social media
Still not found what you’re looking for?